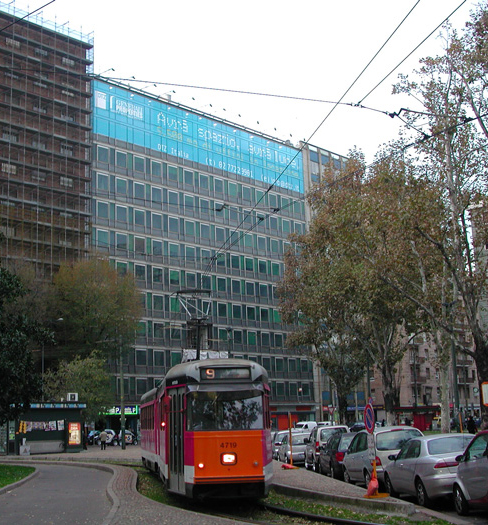
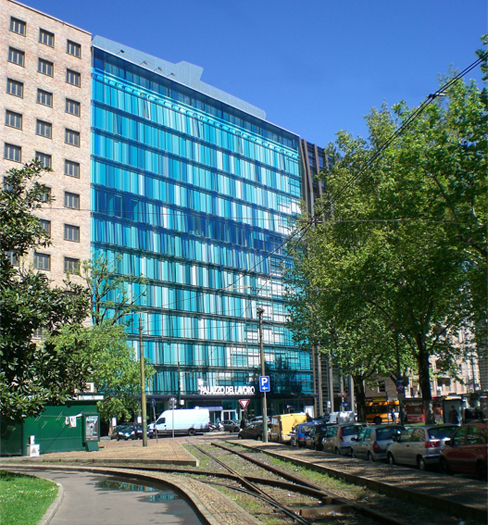
Offices building refurbishment in IV novembre square
Customer: Generali Properties
Years: 2009 – 2011 (Built)
Activities: Preliminary and Detailed Design (Structural and MEP Engineering), Control of worker’s safety on site (HSE), Support to Project Management, Site Supervision (Structural and MEP Engineering), Cost Estimate, Quantity Survey and Value Engineering, Façade Design, Energetics, Fire Engineering, Acoustics
Project cost: Euro 10.5 mln of works
Architecture: 5+1 AA _ A. Femia e G. Peluffo
The property, with a purely executive destination, is located in close proximity to the Central Station and the Pirelli skyscraper. The building’s state of obsolescence necessitated a complete redevelopment.
The project redesigned the architectural image of the building, adapting it to the new quality and performance standards required by the market. This goal was pursued through the renovation of the envelope, all plant components as well as the reorganization of the floors.
The redesign of the elevation on Piazza IV Novembre represented the most substantial intervention, both architecturally as well as functionally and energetically. Of considerable impact and representativeness, the new façade, with a surface area of 1,720 square meters, is visible from such privileged positions in the city of Milan as the Central Station and the Pirelli Skyscraper and, for this reason, can be considered a kind of “vertical square.” It consists of a double ventilated glass skin that runs from the second floor to the roof and is composed of individual glazed modules inserted within the spans of the pillars. It was precisely the treatment of the glass modules that constituted the main architectural characterization of the elevation, as the scanning of three different types of glass, mirror, clear and blue, resulted in the dual effect of reflection and color mutation that gives the building a specific identity.
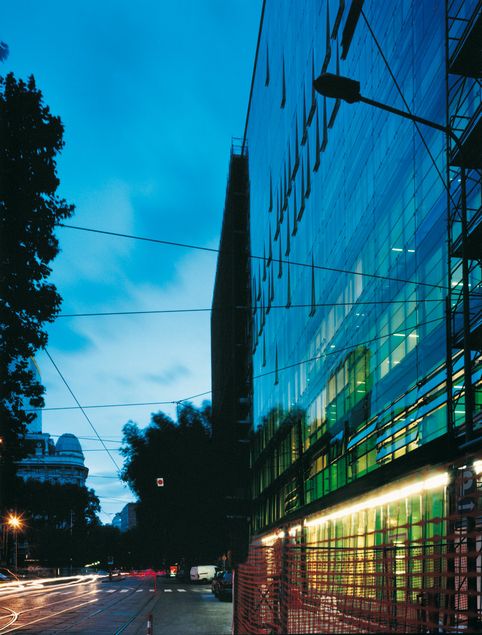

The façade
The double-skin façade is designed to maximize energy efficiency and the thermal, visual, and acoustic comfort of users. It consists of the following layers:
- An interior façade fixed inside the existing floor slab with a profile embedded in the floating floor, consisting of fixed window frames and in number of one for every three casement and vasistas opening French windows with maintenance blocking. The window and door frames are thermal break aluminum, the expected sound reduction is 42dB.
- A motorized solar shading system consisting of blinds made of technical outdoor fabric that can also be operated manually.
- The continuous ventilated cavity, accessible and walkable for maintenance on each floor, performs the important function of ventilation, created for the purpose of regulating energy input and climatic comfort depending on the outdoor temperature.
- The glazed outer skin consists of individual laminated glass modules with a selective component, placed vertically and horizontally. Approximately 30 percent of these modules can be opened automatically to allow for ventilation or insulation of the façade, so that thermal energy can be dissipated or retained, depending on the need to heat or cool the interior spaces, with high levels of energy savings and environmental comfort. The scanning of the module, originated from the decomposition of the spacing of the existing structure, allows the structural pitch of the pillars to be managed, as well as the modularity of the internal arrangements, the supporting carpentry, the internal skin, the curtains, the lights the vents and fancoils, are all elements managed with the pitch of the facade, with rigor and precision.
The plants
The upgrading of the building aimed to achieve a few main objectives. First, the achievement of high energy savings while maintaining a high standard of environmental well-being. This was achieved by working on two fronts:
- the building envelope, so as to make it energy efficient and compliant with recent energy regulations;
- the choice of the latest generation of machinery with a control system capable of limiting waste and maximizing the efficiency of the plant itself.
Secondly, since the building in question was being used for offices, and as such needed the possibility of following the demand for reorganization of work spaces at all times, a development of the plants was studied at the design stage to ensure the least possible inconvenience to users and at the same time the greatest flexibility of reorganization.
Finally, it had become necessary to reorganize technical spaces as a result of both the implementation of facilities (e.g., fire-fighting systems with associated power plants and storage tanks, generator set, etc.) and the relocation of existing technical rooms located in functionally incorrect areas.
Achievement of the previously stated requirements was achieved by the following measures listed in alphabetical order: building management; double-skin façade with integrated dynamically insulated shading; flexibility and modularity of systems; water-cooled chiller units with high COP and partial condensing heat recovery; modular type condensing boilers with low water content and high degree of power modulation; variable air handling units; energy recovery from exhaust air; free-cooling cooling; external shading control system; lighting control system.
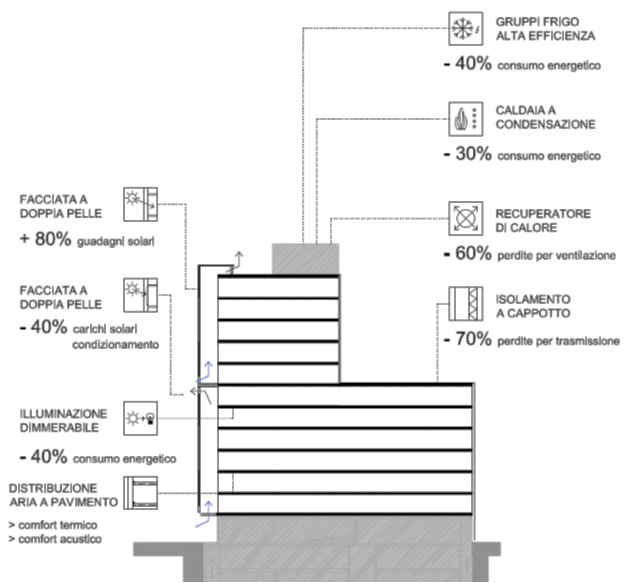
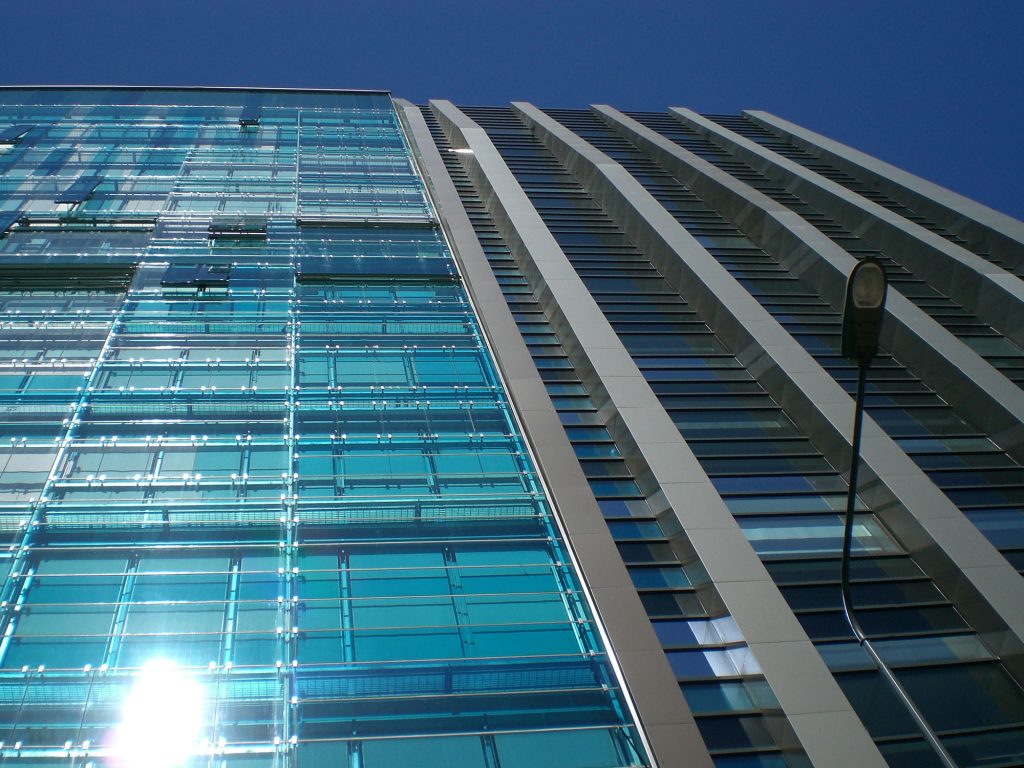
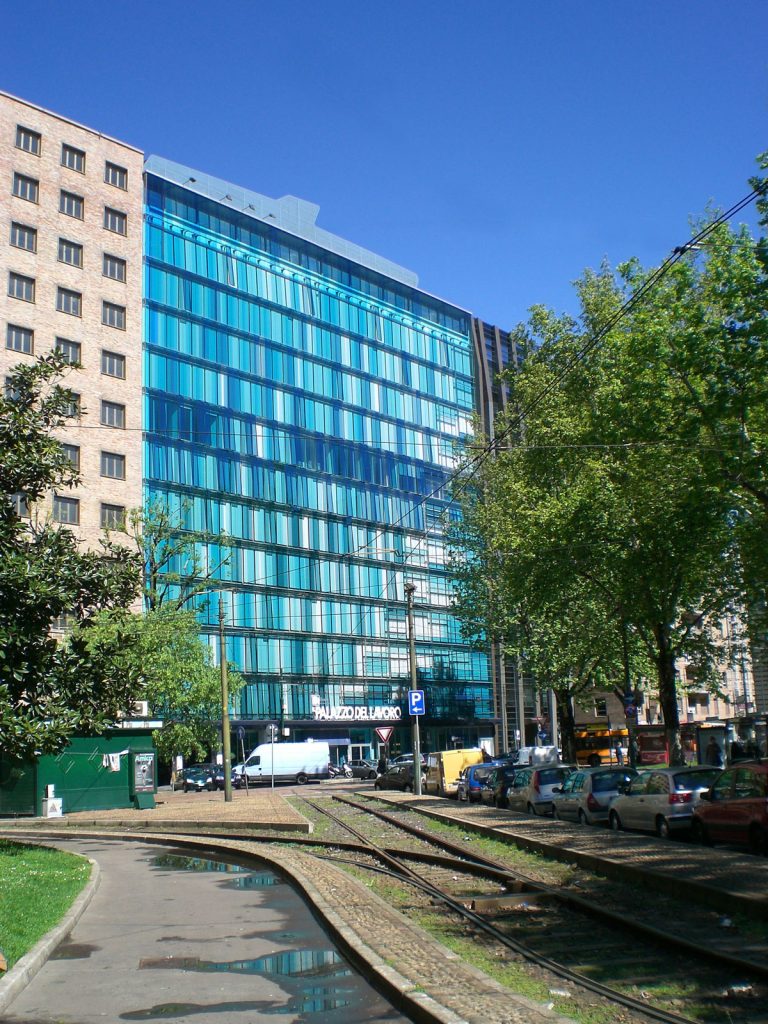
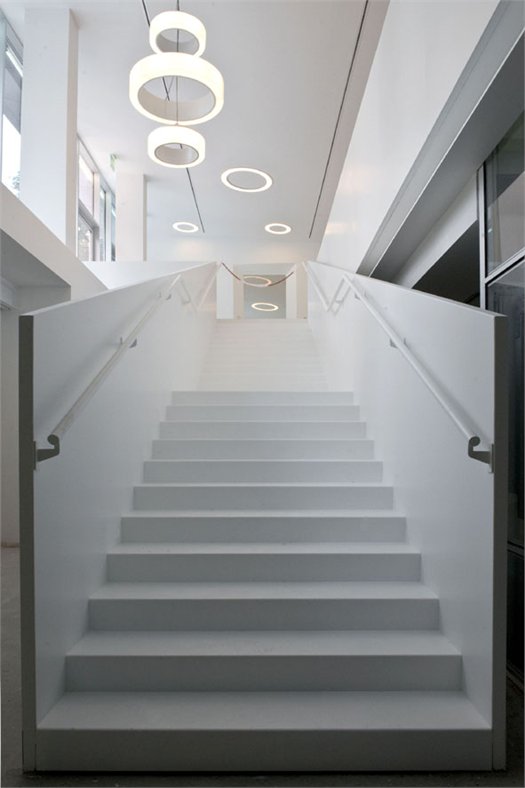
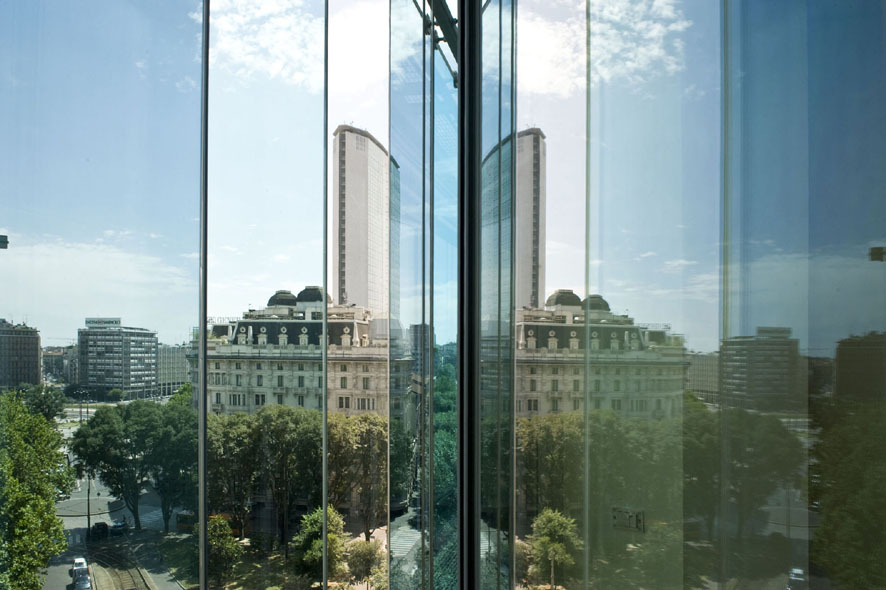
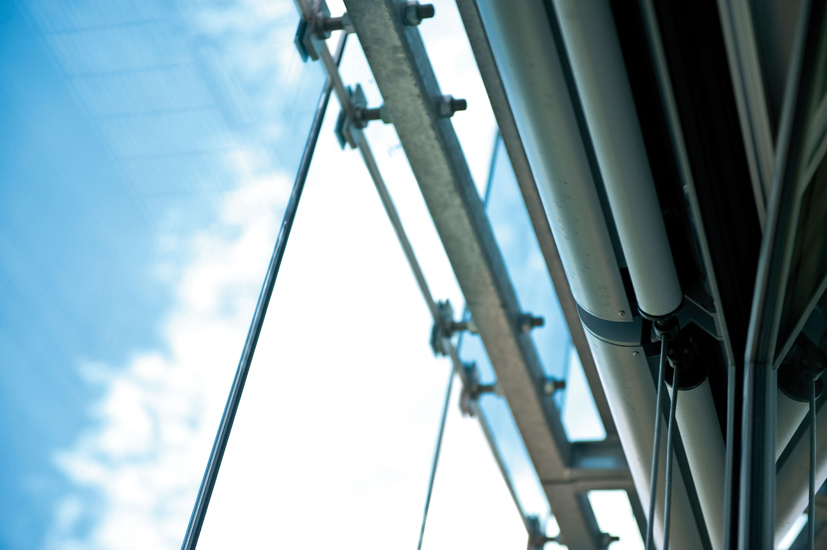